Plastic extrusion for high-volume custom plastic parts
Plastic extrusion for high-volume custom plastic parts
Blog Article
Comprehending the Basics and Applications of Plastic Extrusion in Modern Manufacturing
In the world of contemporary production, the strategy of plastic extrusion plays a critical duty. Unwinding the principles of this process discloses the real adaptability and potential of plastic extrusion.
The Basics of Plastic Extrusion Refine
While it may appear complex, the basics of the plastic extrusion procedure are based on relatively uncomplicated concepts. It is a manufacturing process in which plastic is thawed and then shaped into a continuous profile with a die. The raw plastic product, typically in the form of pellets, is fed into an extruder. Inside the extruder, the plastic undergoes heat and pressure, causing it to thaw. The liquified plastic is then required with a designed opening, referred to as a die, to develop a long, continual item. The extruded item is cooled down and after that cut to the wanted size. The plastic extrusion procedure is extensively used in various industries as a result of its cost-effectiveness, effectiveness, and flexibility.
Different Kinds of Plastic Extrusion Methods
Building upon the fundamental understanding of the plastic extrusion process, it is essential to check out the numerous methods associated with this manufacturing approach. The two key techniques are profile extrusion and sheet extrusion. In account extrusion, plastic is melted and developed right into a continual profile, frequently made use of to develop pipelines, poles, rails, and window structures. On the other hand, sheet extrusion produces huge, flat sheets of plastic, which are normally further refined into items such as food product packaging, shower curtains, and automobile parts. Each technique needs specialized equipment and precise control over temperature and pressure to make sure the plastic keeps its form throughout cooling. Understanding these techniques is essential to making use of plastic extrusion effectively in check my reference modern production.

The Duty of Plastic Extrusion in the Automotive Industry
An overwhelming majority of parts in contemporary vehicles are products of the plastic extrusion process. This procedure has actually reinvented the vehicle sector, changing it right into an extra reliable, economical, and flexible production industry. Plastic extrusion is mainly made use of in the production of numerous vehicle components such as bumpers, grills, door panels, and dashboard trim. The process offers an attire, constant result, making it possible for suppliers to generate high-volume get rid of great precision and marginal waste. The agility of the extruded plastic parts adds to the overall reduction in vehicle weight, enhancing gas performance. The longevity and resistance of these parts to heat, cold, and effect boost the durability of vehicles. Therefore, plastic extrusion plays a critical function in auto manufacturing.

Applications of Plastic Extrusion in Durable Goods Manufacturing
Past its considerable influence on the auto market, plastic extrusion proves just as reliable in the realm of consumer products manufacturing. The versatility of plastic extrusion permits producers to create and generate complex shapes and sizes with high accuracy and performance. The adaptability, adaptability, and cost-effectiveness of plastic extrusion make it a recommended selection for lots of consumer products manufacturers, contributing dramatically to the market's growth and development.
Environmental Effect and Sustainability in Plastic Extrusion
The pervasive usage of plastic extrusion in producing welcomes examination of its environmental effects. Reliable equipment lowers power usage, while waste management systems reuse scrap plastic, decreasing raw product demands. Regardless of these renovations, even more advancement is required to minimize the ecological footprint of plastic extrusion.
Final thought
Finally, plastic extrusion plays an essential duty in contemporary production, especially in the automobile and durable goods industries. Its flexibility enables for the manufacturing of a large range of elements with high accuracy. Furthermore, its potential for recycling check my blog and advancement of eco-friendly materials offers an encouraging method towards sustainable techniques, thus resolving ecological problems. Understanding the essentials of this process is key to maximizing its applications and advantages.
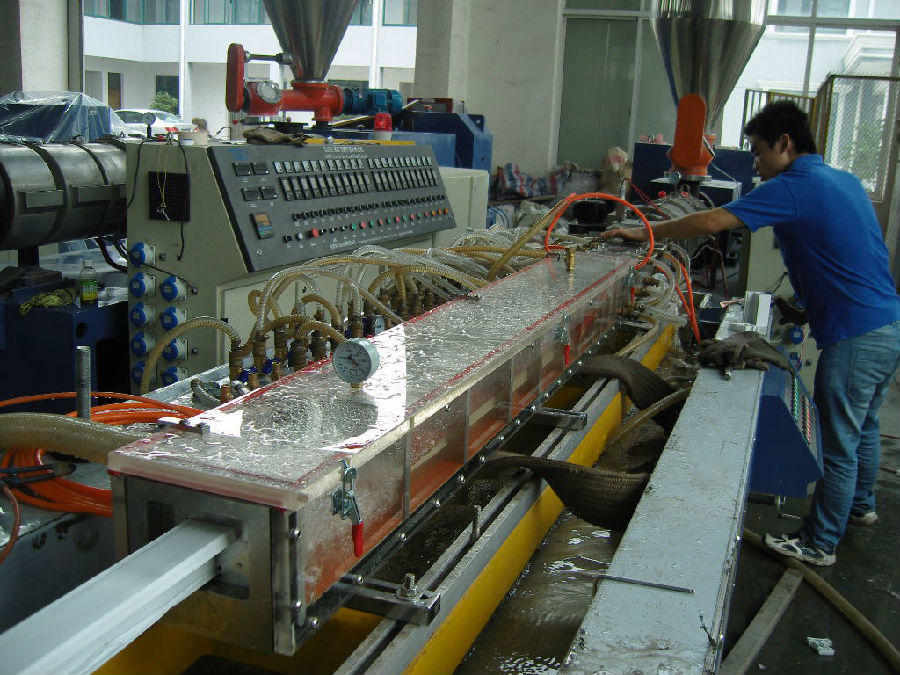
The plastic extrusion procedure is thoroughly utilized in numerous industries due to its performance, cost-effectiveness, and adaptability.
Building upon the fundamental understanding of the plastic extrusion procedure, it is required to check out the numerous techniques entailed in this manufacturing technique. plastic extrusion. In contrast, sheet extrusion produces big, flat sheets of plastic, which are normally further refined right into products such as food packaging, shower drapes, and automobile look at these guys components.An overwhelming bulk of parts in modern automobiles are products of the plastic extrusion procedure
Report this page